Pantex Blog
Wild Pantex – Bird of the Day: American Bald Eagle
Article by Jim Ray, Pantex Wildlife Biologist/Scientist
Who doesn’t love bald eagles? My first exposures to them were the several that spent the winters at Lake Rita Blanca near my hometown of Dalhart, TX, when I was growing up. During those months each year of my childhood, it was a big deal to see this majestic bird. They’d be perched in a tree, sitting on the ice, or soaring above the lake. If the latter, the thousands of Rita Blanca’s ducks and geese would whirl around in the sky above the lake with nervousness.
Later, it was my job with the Texas Parks and Wildlife Department to count them each winter as part of my duties as the Migratory Birds and Wetlands Biologist for this region. During ground and aerial surveys, I’d find them often in association with concentrations of waterfowl. The most I ever saw in a small area was ~40 that were congregated near a large waterfowl (ducks and geese) roost numbering near 180,000 birds. There, they were feeding on sick and dead ducks and geese that were victims of the waterfowl disease, avian cholera.
At Pantex, the bald eagle can be readily seen around our playa lakes and our prairie dog colonies during the winter months. Similar to playa lakes providing concentrated sources of waterfowl for them, prairie dog colonies provide prey in the form of prairie dogs, rabbits, and mice and rats; many of which are snatched from smaller, faster birds of prey. In the fall and spring, snakes likely contribute to their diet. You may spy a bald eagle flying overhead, practically anywhere.
Bald eagles nest throughout much of the U.S., but particularly in the north and in the Gulf Coast States. Until recently, the last known nest in the Panhandle was more than 50 years ago. However, a pair has nested in the Dalhart area, annually, over the last several years. Most nests are near water, where the young are fed heavily on fish. However, the Dalhart nest is not associated with water and the U.S.G.S. Cooperative Fish and Wildlife Research Unit at Texas Tech has found that the young are fed primarily on prairie dogs, cottontails, and black-tailed jackrabbits.
Bald eagles get their white head and tail when they are five years old. These contrast greatly with their very dark body plumage. Juveniles are also darker then the golden eagles they may resemble. Keep your eyes peeled – chances are that during the winter months you will have an opportunity to see a bald eagle. I have even seen them flying right over town. Our nation’s symbol is fairly common here; in fact, it is one of the Texas Panhandle’s best kept wildlife secrets.
Photo: A bald eagle perches on a power line pole overlooking the Pantex Waste Water Treatment Facility.
Wild Pantex – White-tails and Mulies
Article by Jim Ray, Pantex Wildlife Biologist/Scientist
I grabbed a cup of coffee, hopped into my pickup, and headed out towards what we refer to as the Playa 1 Playa Management Unit. It’s just a quarter of a mile or so up the road from my building. I pull over to the shoulder and watch as several pheasants flush from the sorghum stalks to my right into the grassland cover situated across the road and to the left. It is there that I notice a nice mule deer buck that is working his way downslope towards the heavier cover of Playa 1. He’s alone this time, but usually associated with a handful of mule deer that can be seen pretty regularly in this vicinity. Across our 18,000 acres there are a few other places that mule deer associate with, and like elsewhere in the region this time of year, fields of winter wheat can concentrate them.
And then there are the white-tailed deer. This is where I am intrigued.
Growing up, there were very few white-tailed deer in this plains country. In fact, my mention of them being present in the western Canadian River drainage sparked interest from one of my Texas Tech professors and this led to an aerial survey, my first magazine publication (co-authored with the professor), and talk of a M.S./Ph.D. project that would include the professor’s former mule deer-only study sites.
All of this really hit home to me about a decade later when I was running a roadside pheasant survey in the Pantex-like wheat-sorghum-corn-playa country up near Etter in Moore County. That morning I counted more white-tailed deer than I did pheasants. On and around Pantex, mule deer numbers exceed those of white-tailed deer, but still white-tails are a regular inhabitant of the facility.
Although documented in the past, deer observations became commonplace on Pantex beginning in 2003. Enough vehicle-deer collisions have occurred that we now have “watch for wildlife” signs at each entrance and deer crossing signs at other key locations. This fall, conversations indicate a general belief that our deer numbers are way up this year. Our observations don’t support that. We can still go out to certain places and see small groups of deer; certainly not everywhere, or in unprecedented numbers.
A lot of the recent observations are likely more due to where some of the deer are operating and that we have entered a period when deer activity typically increases. Crop harvests have affected available food and cover, as may the first killing frosts, causing deer to move into new areas or make longer trips to food sources. In addition, the advancing breeding season also has a big effect on deer activity.
My friend Calvin Richardson of the Texas Parks and Wildlife Department (TPWD) tells me that their surveys to the north of the Plant in the Canadian River breaks and basin reveal about a 125-175 acres/deer. For comparison, high deer densities in Central Texas can exceed 5 acres/deer. As expected, as you come up out of the Canadian River basin into the flat cultivated country the numbers drop way off.
Here at Pantex, we have run a set of three 24-mile spotlight surveys each fall since I arrived in 1999 and our terrain is wide open, with high visibility. Our first recording of a deer on this survey was in 2004, and the highest number that we have observed since that time is 20. I fully understand that deer come and go, and thus numbers fluctuate, but the highest deer density estimate that I can come up with is 900 acres/deer. Regardless whether that is a high or a norm, this is very believable considering our habitat, Mr. Richardson’s remarks, and where and how many deer we see during our travels.
The fact is the High Plains of the Texas Panhandle have become deer country, and what a beautiful sight they make in our wide-open, flat terrain. However, wherever you may have to drive, be observant for deer and drive safely.
Photo: A mule deer buck photographed at Pantex.
Capitol Christmas Tree Visits Amarillo
B&W Pantex Employees Help Welcome Tree
B&W Pantex employees serve snacks to attendees at an event celebrating a visit from the 2013 Capitol Christmas Tree. The 88-foot tall Engelmann spruce was harvested from the Collville National Forest in Washington and will be erected at the Capitol Building. Babcock & Wilcox was one of the corporate sponsors of the tree tour which will make 22 stops, including Amarillo, before arriving in Washington D.C.
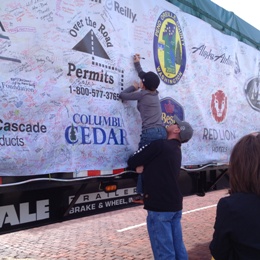
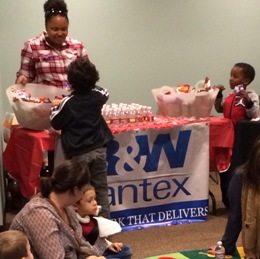
Pantex Night at Discovery Center
More than 500 Pantexans and their families attended Pantex Night at the Don Harrington Discovery Center Sunday. Pantex volunteers served hamburgers and hot dogs at the science center event, which featured an exhibit on the extinct Megalodon shark, as well as a mummy in the Lost Egypt exhibit. B&W Pantex sponsored the shark exhibit.
Wild Pantex - Nuisance Animals: Wrong Place, Wrong Time
Article by Jim Ray, Pantex Wildlife Biologist/Scientist
I had just got to work, settled in at my desk, read a few e-mails, and then my phone rang. The caller proceeded to tell me they were trying to work, but were interrupted by the presence of a rattlesnake. I strapped on my snake leggings, hopped in my truck and headed out toward the location, which involved a 10-15 minute drive.
Actually, snake calls are not that uncommon at Pantex. After all, we are situated out in the prairie. Most nuisance snake calls involve the prairie rattlesnake, bullsnake or checkered gartersnake. But, sometimes it will be an oddity. For example, the only eastern hognose snake ever documented at Pantex was captured in a building during a similar nuisance animal response.
Upon arrival where the rattlesnake was, several workers helped direct me to the snake, which was coiled in a dark corner of the building. True to form, it was a prairie rattlesnake which is the only rattlesnake species documented at Pantex, or that would even be expected in our habitats. With snake tongs, I safely captured it and placed it in a five gallon bucket. I carefully slid a second bucket down into the first, creating a safe holding container for the snake.
Our nuisance animal management program is guided by the Management Plan for Nuisance Animals at Pantex Plant, which was approved by Pantex’s National Nuclear Security Administration Production Office. So, what makes an animal a nuisance? As regards native animals, our use of the term “nuisance” applies only to situations; in other words, when an animal is impacting work, is in a location that is of cause for concern or is acting in a manner that is a cause of concern. Usually, the animal is fine; it is just in the wrong place at the wrong time.
The rattlesnake, of course, has special considerations because it is venomous. But, had the rattlesnake simply been observed crossing a road out in the backcountry, even it would have been left alone. Meanwhile, the peaceful mourning dove sitting on a nest located on the engine block of an important piece of equipment might be considered a nuisance until the pair successfully fledge their young. Other common nuisance animal situations at Pantex include striped skunks under buildings, the presence of feral cats or stray dogs, feral pigeons nesting over work areas and cottontail rabbit and wood rat damage to vehicle wiring.
When we need outside support with situations, we have a great relationship with the U.S. Department of Agriculture’s Wildlife Services, the Texas Parks and Wildlife Department and the U.S. Fish and Wildlife Service. We hold a permit from the Texas Parks and Wildlife Department to trap and relocate nuisance fur-bearing animals, such as raccoons and opossums.
I just never know what a day may hold in terms of nuisance animal situations. Some days I may be able to focus on research or other “planned tasks,” while other days may find me responding to different nuisance animal calls, including setting traps and moving animals. As for today’s subject rattlesnake, following capture, she was transported to a prairie dog colony a few miles to the west and released unharmed.
Please feel free to share this link with others that enjoy wildlife or that appreciate entities that take great strides to contribute to wildlife conservation.
Photo: This large, although harmless, eastern hognose snake was captured on a nuisance animal response trip and relocated to suitable habitat on Pantex. This individual remains the only one of its kind ever documented at Pantex.