Pantex Behind the Scenes: On the Shop Floor
Fabrication capabilities and skillset unique to Enterprise
In a little-known world deep within Pantex, parts and tools are machined to perfection - in one instance to within 39 millionths of an inch - to ensure the absence of variation. Perfection is sought because these aren't just any parts and tools. They are fabricated, modified and repaired for work on nuclear weapons.
"Everything we do is related to a weapons process or supports it in some form or fashion," said Danny Brito, Production Tooling section manager. "Some of the tooling we fabricate is classified and must be made on Plant site. Onsite facilities allow for availability of resources and quick turnarounds."
Tools and packaging created at Pantex to service and protect our nation's nuclear deterrent at times require the use of unique processes and materials made exclusively at Pantex.
One such process used specifically by Pantex in the Machine Shop is called Lumiclading. It coats and protects aluminum alloys, is electrically conductive and provides a smooth and durable finish suited for use in tooling and tester parts for nuclear weapons. New within the last five years, the Lumiclad black oxide process is in demand both by national laboratories and the United Kingdom.
Working hand-in-hand with the Machine Shop is the Pantex Plastics Shop. Molds for parts are at times created in the Machine Shop, and then sent to the Plastics Shop for use. Other times, the Plastics Shop forms PVC using a vacuum process, then sends it to the Machine Shop to be cut to specification.
"The two craft shops openly discuss any issues and share their vast knowledge to ensure we all are successful as a team," said Jody Elliott, Production Tooling craft supervisor in the Plastics Shop.
Adiprene, the material used most often in the Plastics Shop, was created at the Plant nearly 40 years ago and is specially designed to protect nuclear weapons. With its various colors denoting hardness, or durometer, Adiprene is used to make seals, packaging and tools. Most recognizable of the products may be the red W76 nose cone.
When asked the "coolest" thing made out of Adiprene, Elliott said, "Believe it or not, spatulas to support operations where working with high explosives is a concern."
It's the people behind the products that make the difference, explained John Herrera, Production Tooling craft supervisor in the Machine Shop. "Excellent math skills, blueprint reading skills and computer programming knowledge enable our craftsmen and women to do this kind of work,"
he said.
The Machine and Plastics Shops have built a solid reputation at Pantex and elsewhere for quality, Brito said, adding that the traits shared by these unsung heroes that set them apart are their attention to detail, dedication to their work and holding themselves accountable to produce a high-quality product.
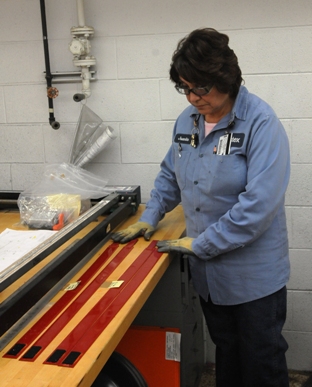
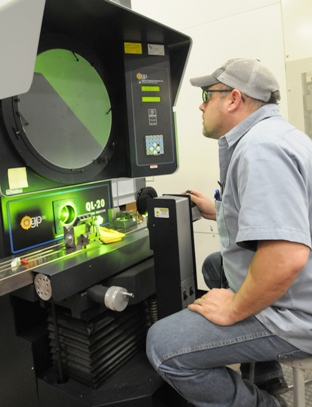