Pantex Blog
Pantexans on the run for Amarillo
At a rapid pace and behind the scenes, Pantex employees are using their passion for running to benefit the Amarillo community.
Scott and Dee Weaver put on their running shoes to help Amarillo charities.
Dee Weaver, an accountant/financial analyst in the Finance and Business Operations Division, has been running competitively since middle school. “I always ran track in school and then back in 2000 I started running 5 and 10Ks,” Weaver said.
It doesn’t matter the size of the race; Weaver has run marathons in Chicago and Fort Worth, just to name a few, and even the Tempe Ironman, but one thing she really enjoys is being able to give back to the community. You can count on Weaver to send emails out to everyone reminding them about upcoming events, such as the Komen Race for the Cure or the TRI to Make a Difference triathlon held annually at Lake Tanglewood.
“I always send out emails letting everyone know about upcoming runs,” Weaver said. “And I always get tons of responses; some people can’t participate in the different events but still want to help. That’s something that never changes — Pantexans’ willingness to help others.”
Thirteen Pantexans competed in this year’s Tri to Make a Difference triathlon by swimming 400 meters, biking 10 miles and running 3.1 miles, all while helping raise money for the Children’s Miracle Network. During the summer, Pantexans also ran to help raise medical funds for a Pantexan’s family member who was battling cancer. “It was a last‑minute run, but many people were able to come together and raise more than $1,000 to help with the medical expenses for this little girl,” said Weaver.
Another member of the unofficial Pantex runners club is Steve Filipowicz, a Facilities Services senior manager. At age 61, he is currently training for his fourth ironman competition.
Steve Filipowicz runs in the TRi to Make a Difference Triathlon.
Much like Filipowicz, Rickey Hook, a facility manager for Waste Operations, enjoys the health benefits that running has to offer. “I was closing in on 50 and had never worked out regularly. I was 50 pounds overweight and took several medications to reduce my lipids and had taken an acid reducing drug for more than 20 years,” said Hook. “I was motivated by my wife, Vickie, to start working out, and not by her nagging or prodding me at all, but because she started and I saw the benefits to her.” Now at age 57, Hook is in excellent health, has lost 50 pounds and is no longer on medication.
Not only is running great exercise, but as Hook pointed out, it is a chance for you to bond with others, and that is something that Weaver enjoys about the activity. She and her husband, who also works at Pantex as a senior manager in Multi-Disciplinary Engineering, train together. “For me, it is so much more than just running — it is about the relationships you make along the journey. My husband, Scott, and I enjoy running and biking together. We help encourage and motivate each other to stay on track, keep pressing forward and cherish every mile together,” Weaver said.
One thing the three emphasize is that people interested in taking up running should take it easy and not get discouraged. “It took years to go from where I was to where I am now. It was a very gradual process but one that has been very gratifying,” said Hook.
Not only is running a physical activity – it is mental as well. “Training is all about building stamina. Sometimes you are out there and it hurts, but you have to push through it,” Filipowicz said. “The races at the Ironman distance, 140.6 miles, are won or lost in your mind. You have to learn how to push yourself through significant discomfort, and it can become very emotional.”
The informal Pantex runners’ club estimates their efforts for fiscal year 2015 have helped raise more than $5,037 by running various distances for local charities.
“I spend about 15 hours a week working out and training,” said Filipowicz. Not only does he enjoy running, but he uses it as a way to stay fit. “I won’t just work out for the sake of working out; running in different competitions gives me a reason to work out, and I need that goal to keep me going.” Apparently his method is working, because he has yet to have any health issues. “I’ve made it to 60 without needing any medications or having any health problems. I would like to keep going in that direction, and I think running is the main reason why I’ve been so healthy,” Filipowicz said.
Pantexans deliver ‘sunshine’ to single parents
A team of Pantex volunteers provided support to families in the Eveline Rivers’ Sunshine Cottages to put healthy meals on the table while the single parents prepared for finals. The cottages are housing for low‑income or homeless single parents who want to finish their education, work and raise their children in a safe environment.
Pantexans Caleb Rejino (left) and Danny Caverly, right, and Colin Caverly, Caverly’s son deliver meals to the Eveline Rivers Sunshine Cottages in Amarillo.
“Finals week can be a difficult time for anyone,” said Pantexan Caleb Rejino. “Eveline asked us to help the Sunshine Cottages by providing pre‑cooked or easy to prepare healthy meals. It is one less thing the parents have to worry about while studying for finals.”
Eveline Rivers, an Amarillo philanthropist, opened the Sunshine Cottages in 2001, with one home that was renovated into apartments. She now has six facilities with the goal to move “the whole family off the government system,” according to Eveline’s Sunshine Cottage website.
Residents of the Sunshine Cottages are required to take at least 12 hours of college classes each semester, work and ensure their children attend school. “These parents are working hard to finish their education and making sure their children learn by example,” Rejino said.
Rejino and members of his team delivered frozen casseroles and other items to the Sunshine Cottages Oct. 21. Rejino said nine members of the team cooked, and four anonymous Pantexans donated money to buy extra items.
The team was funded by Consolidated Nuclear Security. The Pantex Day of Volunteering was postponed so that both Y‑12 and Pantex can join forces next year. Some projects were approved for this year if the work couldn’t wait until 2016.
Pantexan Calvin Nelson secures recognition for expertise
Pantex’s own Calvin Nelson was recently awarded the 2015 Analyst of the Year for Transportation Security by the Department of Energy’s Nuclear Materials Information Program. The award, for which Nelson is the first‑ever Pantex recipient, recognizes outstanding analytic support to the NMIP.
All transportation security analysts and criteria managers working in the program, including the national laboratories, submit nominations to the NMIP Program Management Office in Washington, D.C., where the finalists are selected. “Nominations are submitted based on an individual’s dedication, teamwork and diligence to the program,” said Tommy Butler, director of special programs. “For Calvin to be selected for this award is without a doubt noteworthy of his performance.”
NMIP is a Presidential Directive program, meaning it was one of a few programs that have been briefed to President Obama. Besides covering transportation security, NMIP also covers site security as well as materials properties.
Even with his 30‑plus years of experience at Pantex, Nelson was not expecting to win the award. “I was really surprised when I got the notification that I had been selected,” Nelson said. “It is a great honor, and I’m so proud to have the opportunity to work with some great folks at the labs and at DOE Headquarters. Also, it’s been great to bring some of these folks that I work with to Pantex and show them our unique capabilities.”
Wild Pantex – Bird of the Day: The Dickcissel
Article by Jim Ray, Pantex Wildlife Biologist/Scientist
One of my favorite prairie birds is the Dickcissel. This native sparrow resembles a miniature meadowlark with its yellow breast and black bib. The Dickcissel’s name actually comes from the male's song –they spend a whole lot of time proclaiming their name and territory.
This summer, I had the pleasure of hearing a Dickcissel sing regularly as I walked from my car or work truck to the entryway to my office building. Several times while walking with someone I hollered out, "shhsh, hear that Dickcissel singing?" Of course, there was usually a wait period for the bird to sing again after the question rolled off my tongue. Normally, though, the Dickcissel didn't disappoint and soon announced his presence again.
The term Dickcissel usually puts a smile on the other person's face, maybe because with a name like that they think I must be pulling their leg. My next statement is invariably, "No, I am not kidding. These guys stay here to nest in these wetter years, and this was the second such notable year since I have worked out here.”
This native prairie sparrow likes the taller cover found here during our wetter years. Their nests are a bulky cup of weed and grass stems placed slightly above ground-level in dense grasses or in saplings. The nests are lined with finer grasses, rootlets and hair, upon which three to six unmarked, pale blue eggs are laid.
I first became familiar with the Dickcissel while attending graduate school in South Dakota. I lamented the fact (as a young wildlifer) that the state bird of South Dakota was an exotic bird – the Ring-necked Pheasant. Nevermind how much money the bird brings into the state's economy – state birds in this great nation should be native birds! In a prairie state it should be a good prairie bird!
"Which one," my summer technician once asked.
Since both of us thought that the Dickcissel was a great prairie bird, it was an easy choice! The Dickcissel is a great "bird of the day" designee. It is a welcomed visitor to our Wild Pantex, and the more years that we hear its voice, the better off we all are knowing that rainfall has been abundant here on the shortgrass prairie.
The shortgrass prairie is a productive ecosystem, including for ground-nesting songbirds. In some years, the Dickcissel makes irregular movements outside of its core breeding range to breed in surrounding areas of grassland.
Going pink from Texas to Tennessee
From Texas to Tennessee, Consolidated Nuclear Security employees were in the pink for October. More than 100 employees, friends and family members participated in the Susan G. Komen Race for the Cure in the two locations while other employees wore pink and even dyed their facial hair.
Pantex employees, friends and family members laced up their shoes for the Greater Amarillo Race for the Cure. CNS was a platinum sponsor of the event.
In Texas, about 75 Pantexans, friends and family members, including two breast cancer survivors, participated in the Greater Amarillo Race for the Cure. CNS contributed $2,500 to the Susan G. Komen Amarillo Affiliate as a platinum sponsor of the event and paid for employee registration. Curtis Chamberlain, a production manager, who ran in the event with his 11-year-old daughter, said it was a “good opportunity to spend quality time with her and support a worthy cause.”
In mid-October, Y-12 LiveWise hosted a women’s health fair and encouraged all employees to wear pink for breast cancer awareness. During the fair, employees could receive flu shots, participate in some health screenings and receive health information.
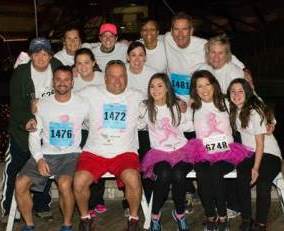
Employees, friends and family members from Y-12 prepared for the Knoxville Race for the Cure in the pre-dawn hours Oct. 24. (Photo by Big Orange Professional Photography)
A few weeks later in Tennessee, 33 Y-12ers joined the cause at the Knoxville Race for the Cure. CNS provided t-shirts for the runners in addition to covering employee registration fee. Shelia Scarfo of Y-12 participated with her two daughters. She said, “I walk with one of my daughters each year since my grandmother died from this disease, and my mother is a survivor.”
One Y-12 employee felt breast cancer awareness was worth significant attention and dyed his beard pink. Rodney Ryder, a lineman in Power Operations, dyed his beard pink noting “I have extended family members who are battling breast cancer.” When he went to a salon to inquire about dying it pink, the stylist agreed to do it (and provide any needed touch ups) for free, given the cause.
Ryder says all the teasing from co-workers is worth it. “When a woman tells me thank you or shares her story with me, I know my purpose of dying it was right. I’m thinking of doing it yearly,” he said.